Certified ISO 9001:2008, ISO 14001:2015
SERVICES
As a fully certified ISO 9001:2008, ISO14001:2015 and TS16949 certification organization, Welson Mold is proud to be a technologically advanced supplier that provides the increased manufacturing capabilities and efficiency our customers demand in injection mould and moulding industry.PRODUCTS
Welson Mold meets all the requirements of manufacturing Automotive, Household appliance, Office appliance, Commodity, Telecommunicationtools and Medical apparatus molds and products. We mainly export our molds and products to Australia, USA, Europe and Brazil.
Who we are
About Welson Mold
Welson Mold (Hong Kong) CO. LTD was founded in 2008, located in 1F, Building A2, Silicon Valley Dynamic Digital Science & Technology Park, ZongYi RD, GuanLan Town, LongHua New District, SHENZHEN( Link to the Google Map )深圳群辉模具有限公司, where our plant is built in the 1600 square meters’ area. Welson Mold is one of the leading suppliers of plastic mold & die casting mold in the world, specialized in providing the solution of OEM service for a wide range molds, mold design, mold testing, mold fitting machining, mold modifying, part optimization and hardware part machining.
- Full Service Custom Injection Molding
- Precision Injection Molding
- Mass Production
- Insert Molding
- Over Molding
- Double Injection Molding
- Unscrewing Molding
- Gas Assisted Molding
- Multi & Single Cavity Molding
- Part Optimization
- Rib and Boss Design
- Dimensional Properties
- Mechanical Properties
- Cost Analysis
- Design For Manufacturability
- CAD/CAM Design
- Mold-flow Analysis
- DFM Report
- Complex Mold Design
- Highly Engineered Work Cells
PROJECTS
HAPPY CLIENTS
QUALIFIED STUFF
MOLDS
OUR SERVICES
Precision Mold
All-Plastics focuses on zero defects by providing premier precision injection molding for high liability componentry. By utilizing scientific decoupled molding techniques, documented process controls and automation, we are able to provide high quality products at a low cost.
Automotive
Automotive injection molding has enhanced the auto industry for decades now, and for good reason. Injection molding provides consistency, high volume and low cost. Converting parts to plastic material can help drive down costs, maintain part strength and at the same time reduce weight over metal parts, which leads to increased fuel efficiency for cars.
Precision Component
Machining is the fastest, most economical way to produce a finished technical plastic component – particularly for small production runs. Plastic injection molding creates precision thermoplastic parts to mold exact shapes and features for use in any application. Engineers, designers, machinists, and production coordinators all played critical roles in the success of a project.
Large Size Mold
Very large moldings, and in particular those with thick cross sections, require extremely specialized heavy duty presses, unique rubber formulations and highly specific production techniques and methodologies. Experience in the unique material compounding techniques is required for the molding of very large articles.
Household Appliance
Home appliances are electrical/mechanical machines which accomplish some household functions, such as cooling/heating, cooking or cleaning. Examples: Coffee machines, refrigerators with complete equipment, including freezer drawers, balconies, components for boards, panels, pumps, connectors, nozzles, applications in special high performance injection materials, e.g. Grivory, Peek, others.
Die Casting Parts
Die casting is a manufacturing process for producing accurately dimensioned, sharply defined, smooth or textured-surface metal parts. It is accomplished by forcing molten metal under high pressure into reusable metal dies. The process is often described as the shortest distance between raw material and finished product. ‘Die casting’ is called ‘pressure die casting’ in Europe.
Double Injection Mold
Double injection molding is a process of producing parts with two different polymers or two different colors during single operation. The process starts with injecting the melt into primary cavity. Then the cavity plate rotates by 180 degree or the primary molding is moved to the secondary cavity. Finally the second color or a different polymer is injected into secondary cavity to fill the space between primary molding and secondary cavity.
Unscrewing Mold
Unscrewing molding is a unique injection molding process with mold technology that includes movement and rotation to produce threaded components. Some plastic parts such as caps and closures with detailed threads cannot be removed using standard knock-off methods. After they are molded, parts need to be carefully unscrewed from mold to avoid damaging the threads.
Multi Cavity Mold
A mold with multiple cavities of the same part that is typically used to reduce piece-part pricing for higher volume parts. Multi-cavity molds are particularly economical in mass production of high quality components. If you want more than tens of thousands of parts per month, then a Multi-Cavity Mold is for you. What you are really buying is machine time. So the less machine time it takes to mold your parts, the less your parts will cost.
WORKING WITH US
We have 80T, 180T, 350T, 550T, 1000T injection molding machines
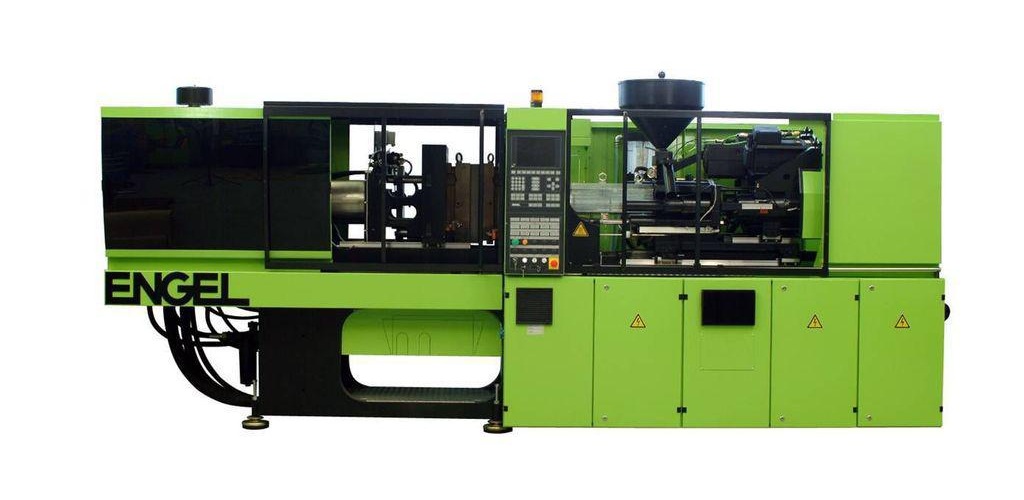
Our news
Our testimonials
Our clients
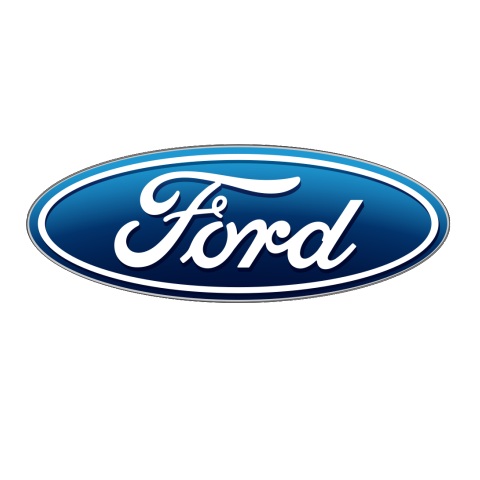
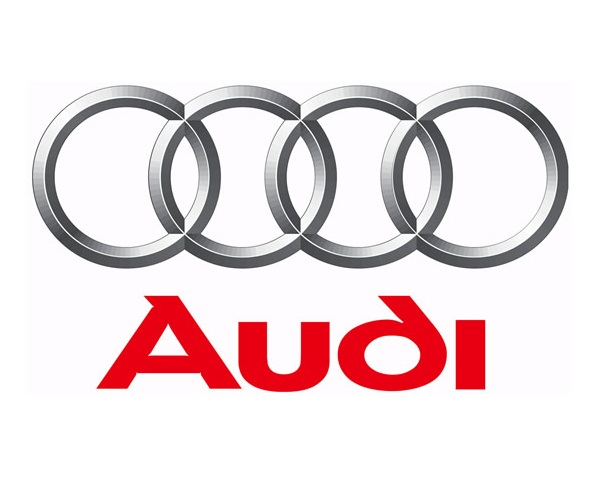
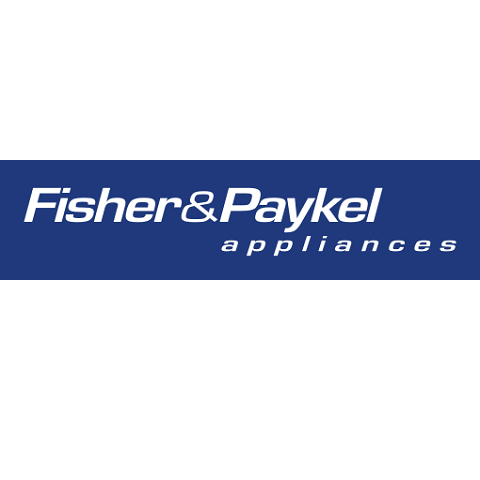
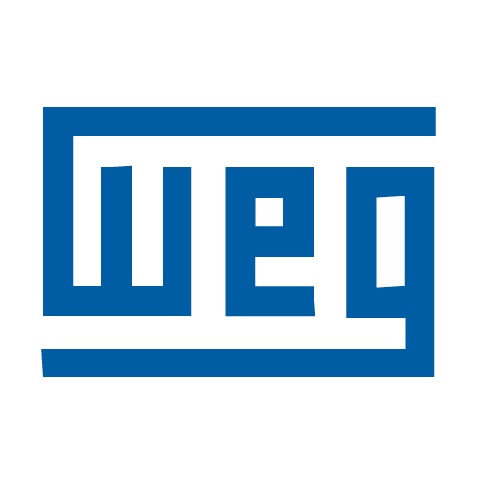
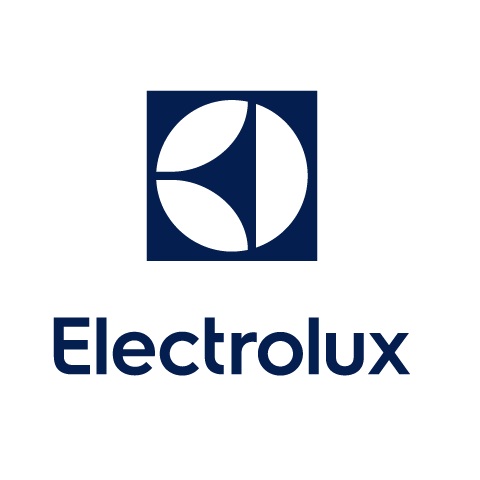
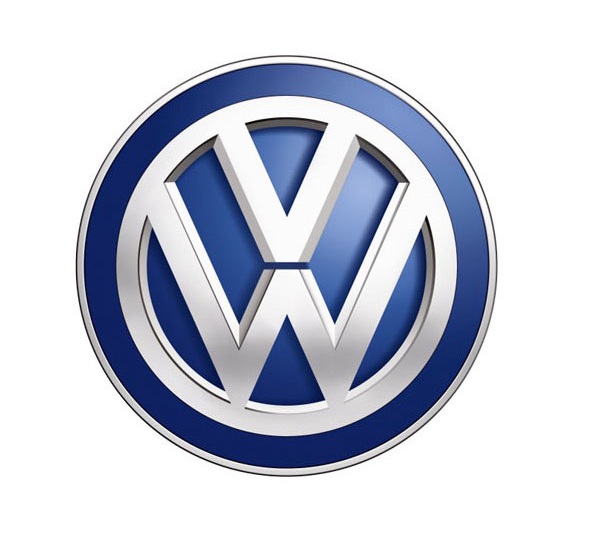